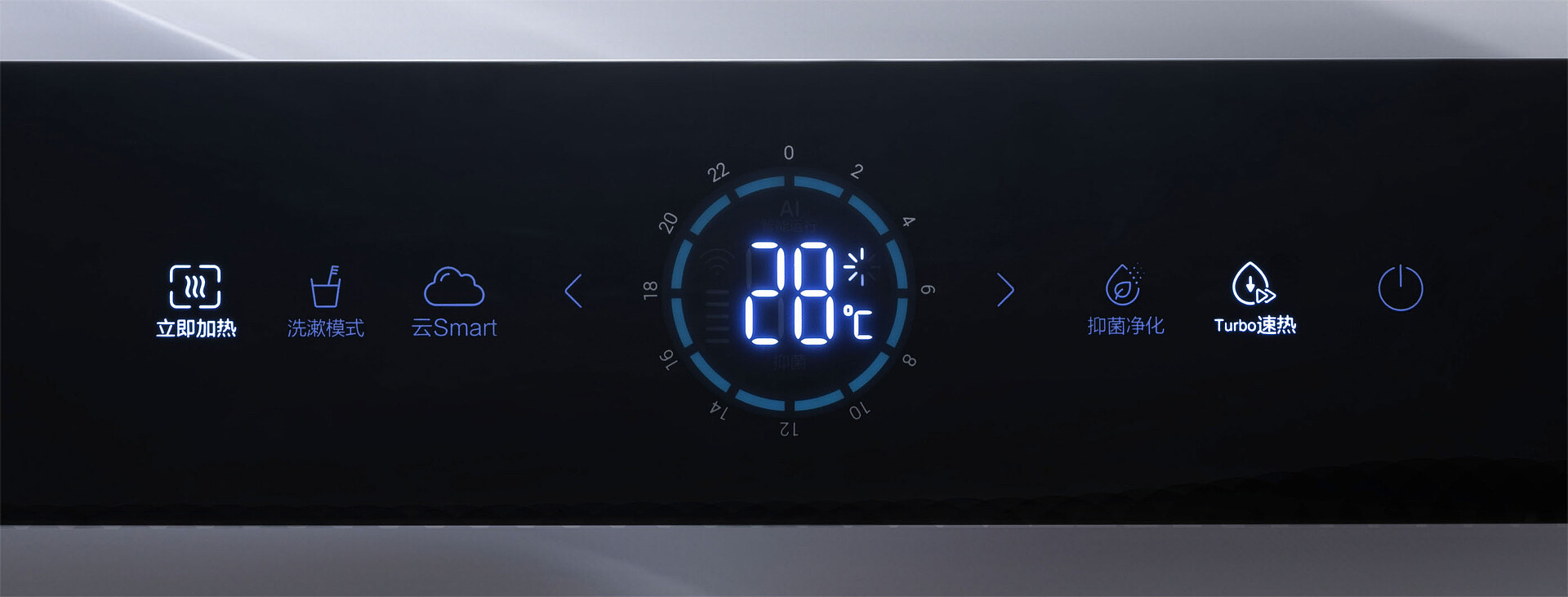
Functional Foil Bonding (FFB)
Transforming complex operating options into an easy-to-understand product: That’s the challenge facing developers and designers today. Customers expect a perfect symbiosis of design and functionality. With the patent-pending Functional Foil Bonding (FFB) process, KURZ combines surface design and sensor functionality on a single component. Functional elements can be seamlessly integrated into the decor and also into three-dimensional part geometries.
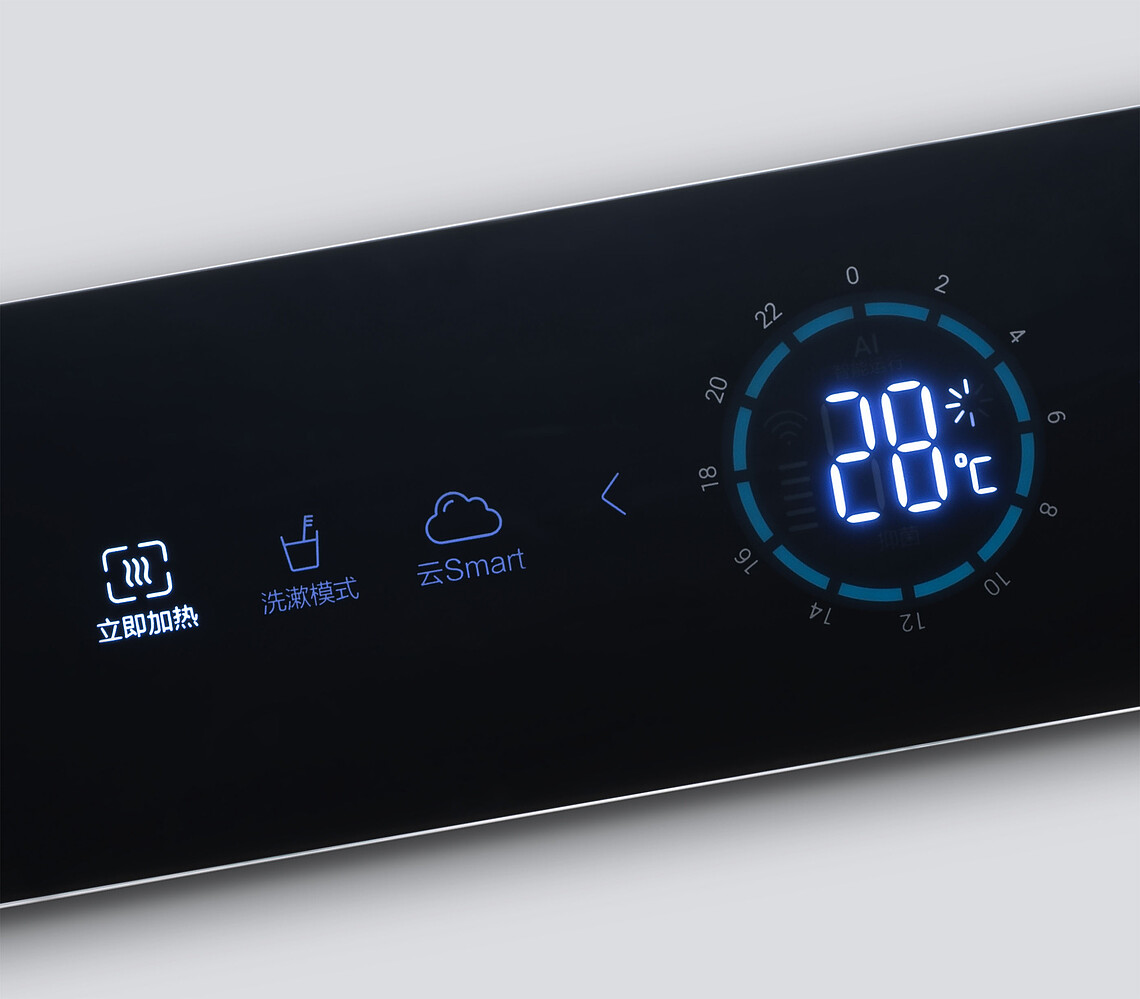
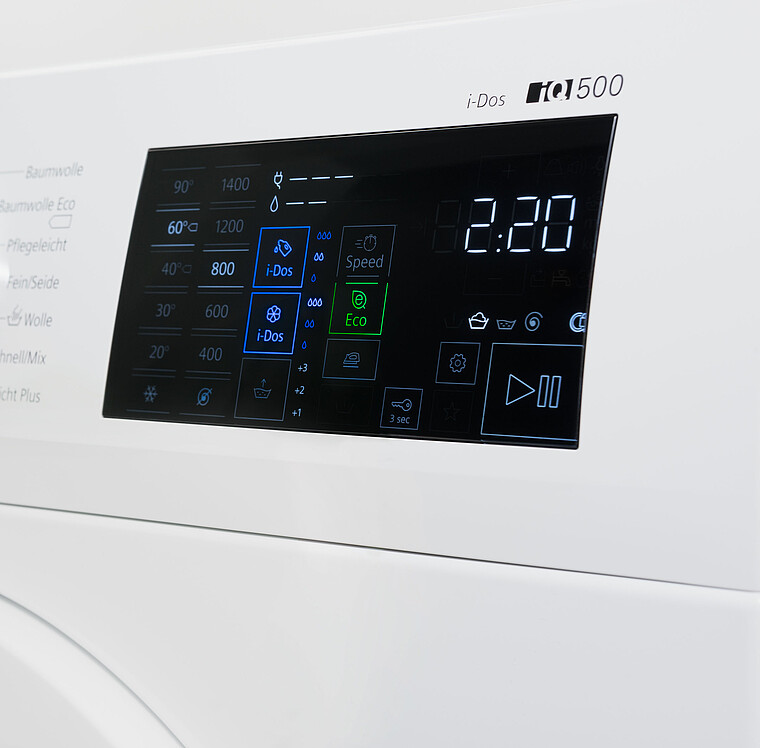
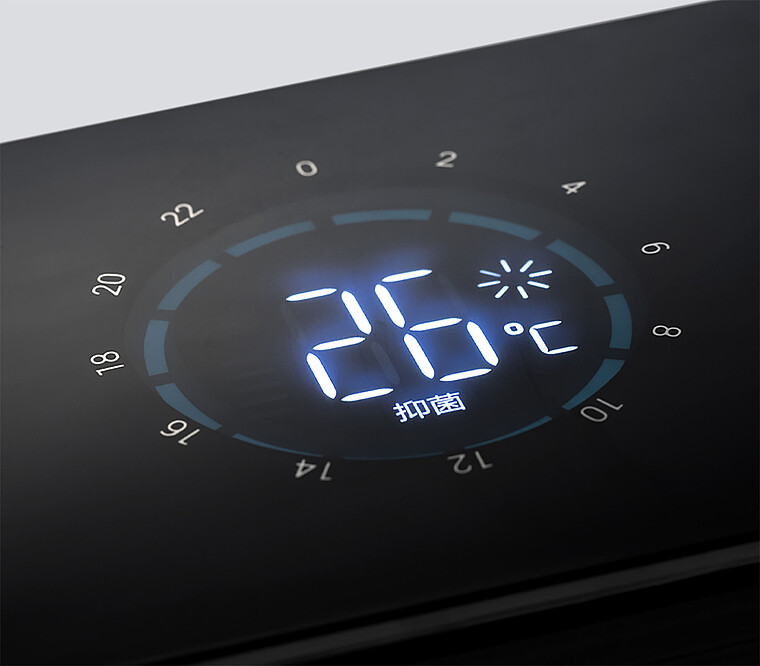
KURZ: Extreme levels of freedom with FFB
Due to their innovative nature, the sensors produced by the KURZ subsidiary PolyIC allow for sophisticated surface designs and fascinating lighting effects with backlighting. Thus, all controls with single- or multi-touch function or gesture control can be arranged directly on the display area. Flawless capacitive operation can be easily realized even with thick plastics.
Small or large volumes: You develop your vision - we make it come true. Our creative design team always has its finger on the pulse of new trends. Because that’s what makes you the partner of choice for your customers - an exceptional user experience.
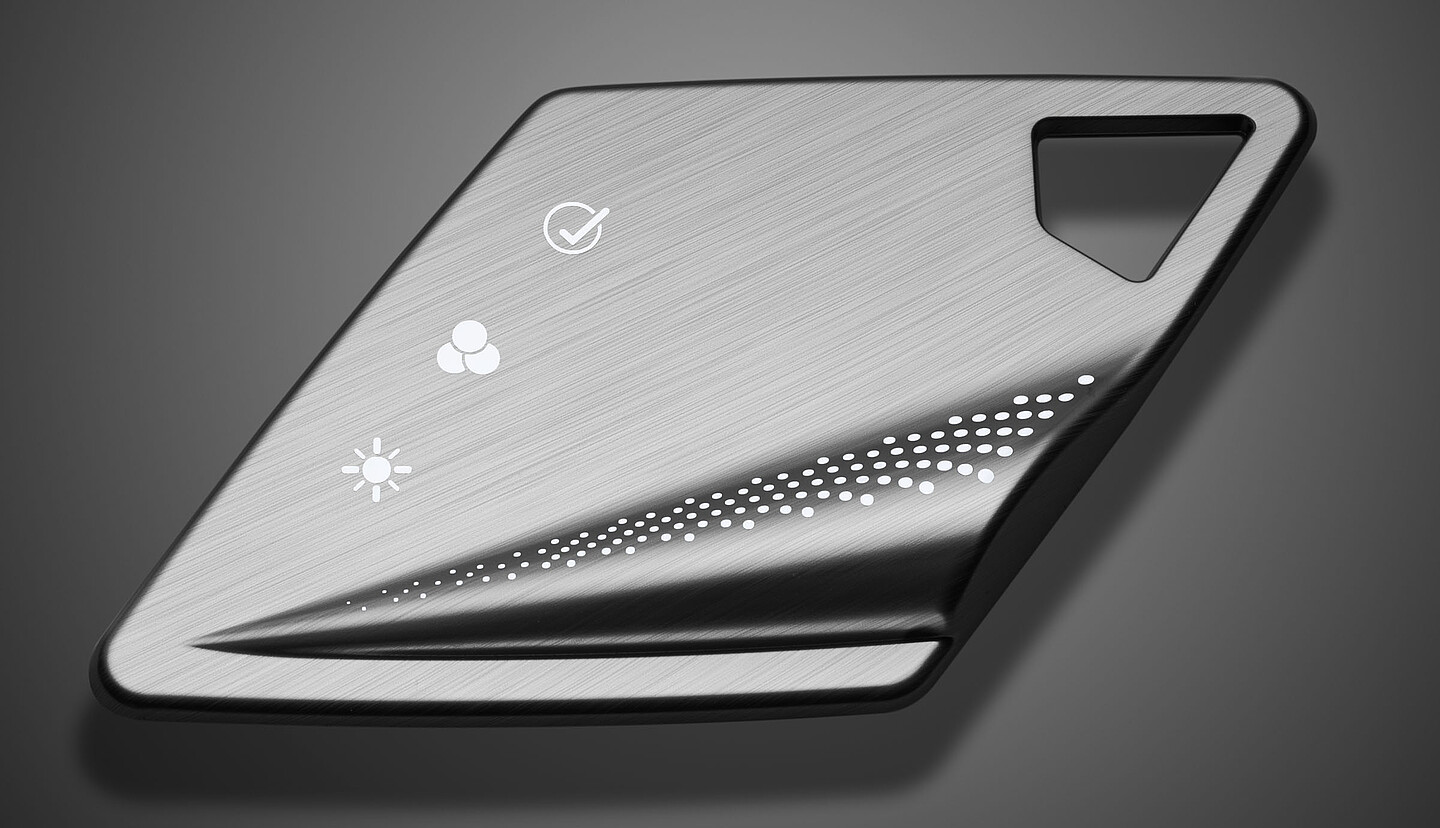
Technically sophisticated, aesthetically pleasing, deceptively real to the touch - Customers want to be emotionally touched and inspired. With Functional Foil Bonding, KURZ has developed a technology that meets the needs of ambitious users. FFB works for almost all plastics and complex geometries, both for display operation and for smart applications. In the process, capacitive PolyTC® sensors made of wafer-thin metal mesh structures are applied to the plastic surface on the back of a component. Highly transparent and radiolucent, they are practically invisible, which plays an important role especially for smart displays.
The Functional Foil Bonding process
Lifting process video
- The ready plastic part is inserted into the machine fully automatically.
- The PET carrier with the metal mesh sensors is placed exactly over the component.
- The heatable embossing stamp moves up and down fully automatically and connects the sensors to the component.
Roll-on process video
- As with vertical stamping, the decorated and shaped component is positioned in the machine. The sensor foil is then aligned precisely over the component.
- A heated stamping wheel lowers and rolls over both components, which are connected to each other by heat and pressure.
The main advantages of Functional Foil Bonding at a glance
- More reliable than conventional processes such as integration through OCA (Optical Clear Adhesives)
- Excellent, constant adhesion
- High optical quality for a wide variety of surface decorations
- Highly transparent and therefore radiolucent
- Meets even high demands on reliability
- Extremely precise positioning of capacitive sensors in the component
- Simple integration of the process into your value chain
- Low additional costs
- Variable processes depending on the value chain