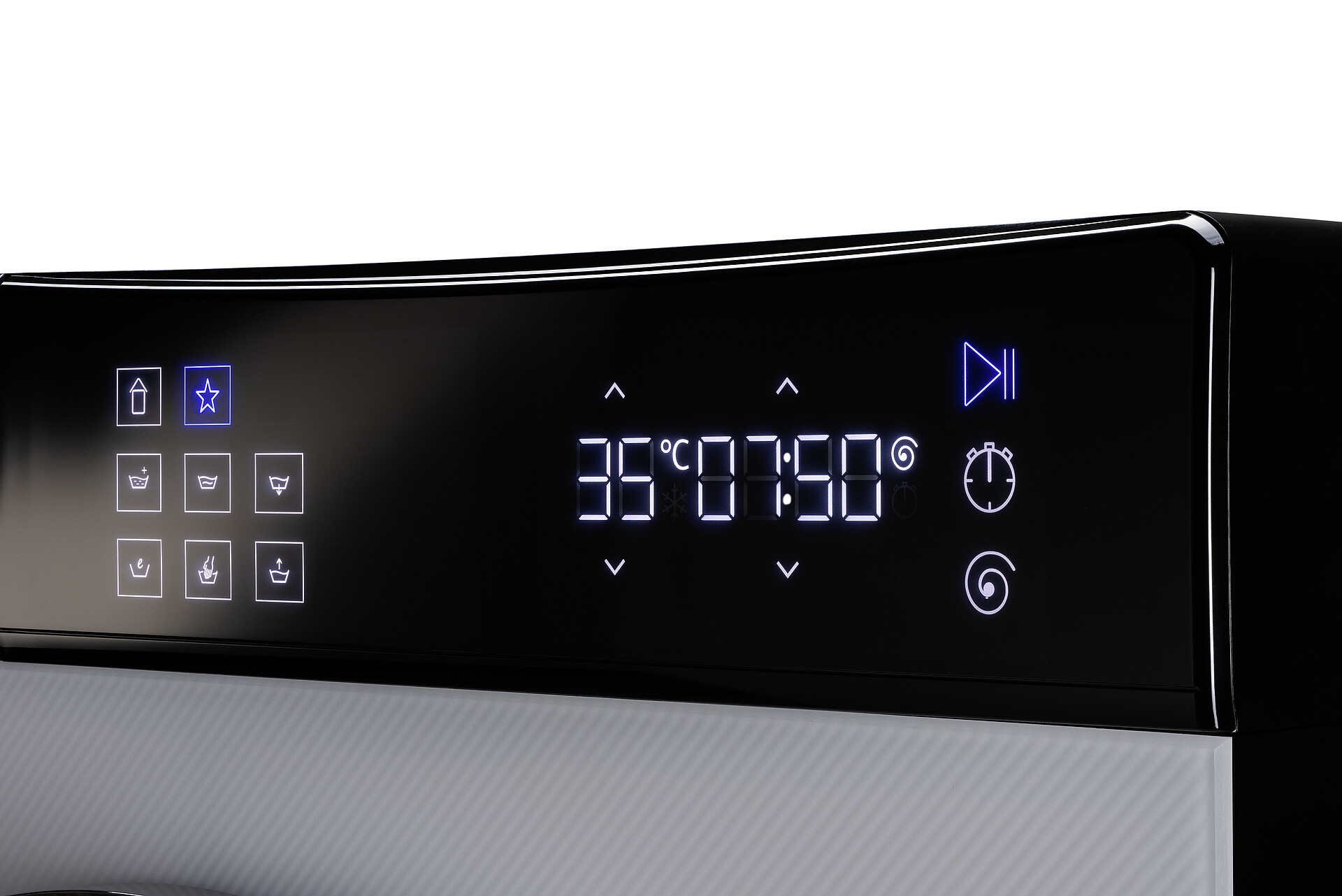
In-Mold Decoration (IMD)
The product design decides whether a customer is prepared to take a second look. KURZ's innovative In-Mold Decoration (IMD) process ensures in a single work step that the surfaces of your products will attract customers as if by magic. IMD gives you extreme freedom in design and feel, while protecting against external influences such as scratches, abrasion, sunscreen, and moisture. A further advantage is that this process reduces your carbon footprint by 70 percent!
The In-Mold Decoration process
A foil feeder such as the IMD SI DUO is mounted on the injection molding machine, which ensures that the decorative foil is exactly aligned
The carrier material with the decoration is pressed onto the wall of the tool cavity with the injection molding compound. Due to the heat in the tool, the decoration detaches from the carrier and is transferred to the component with a strong adhesive bond
With this process, individual image decors of over 1,000 millimeters in length can be applied with extreme precision
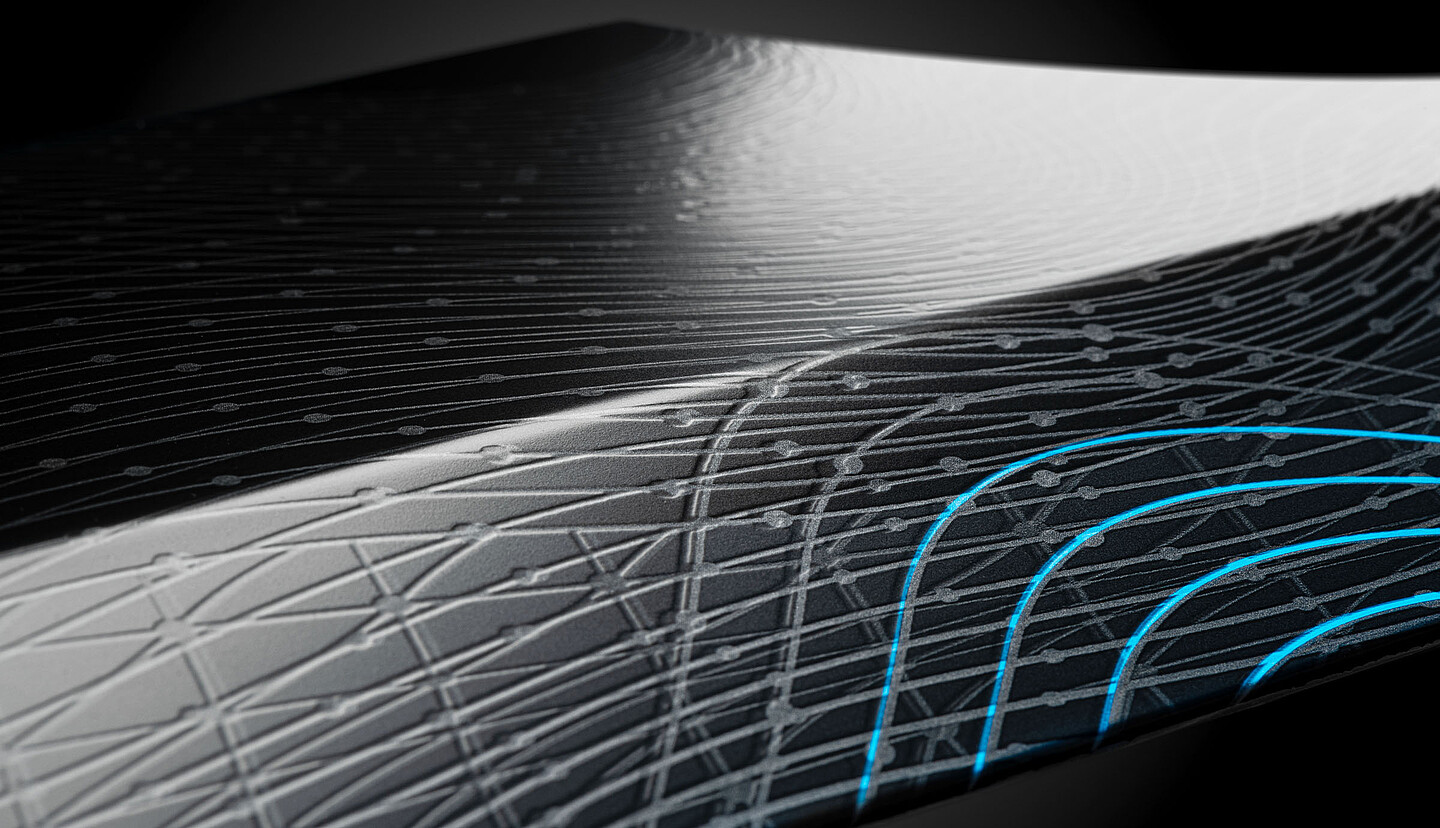
The main advantages of KURZ In-Mold Decoration at a glance:
- Reduction of the carbon footprint by 70%
- Economic integration into your value chain
- Also suitable for complex geometries, such as curved displays or 3D geometries
- Various haptic effects can be achieved with soft-touch surfaces. This gives you an additional competitive advantage, as haptic design is increasingly becoming a distinguishing feature
- Consistent quality, even for large series
- Radiolucent, partial or full surface, day-night design, dead-front design, or ambient lighting
- Metallized decors without shielding Wi-Fi, Bluetooth, or wireless connections. We use non-shielding Non-Conductive Vacuum Metallization (NCVM) films on request
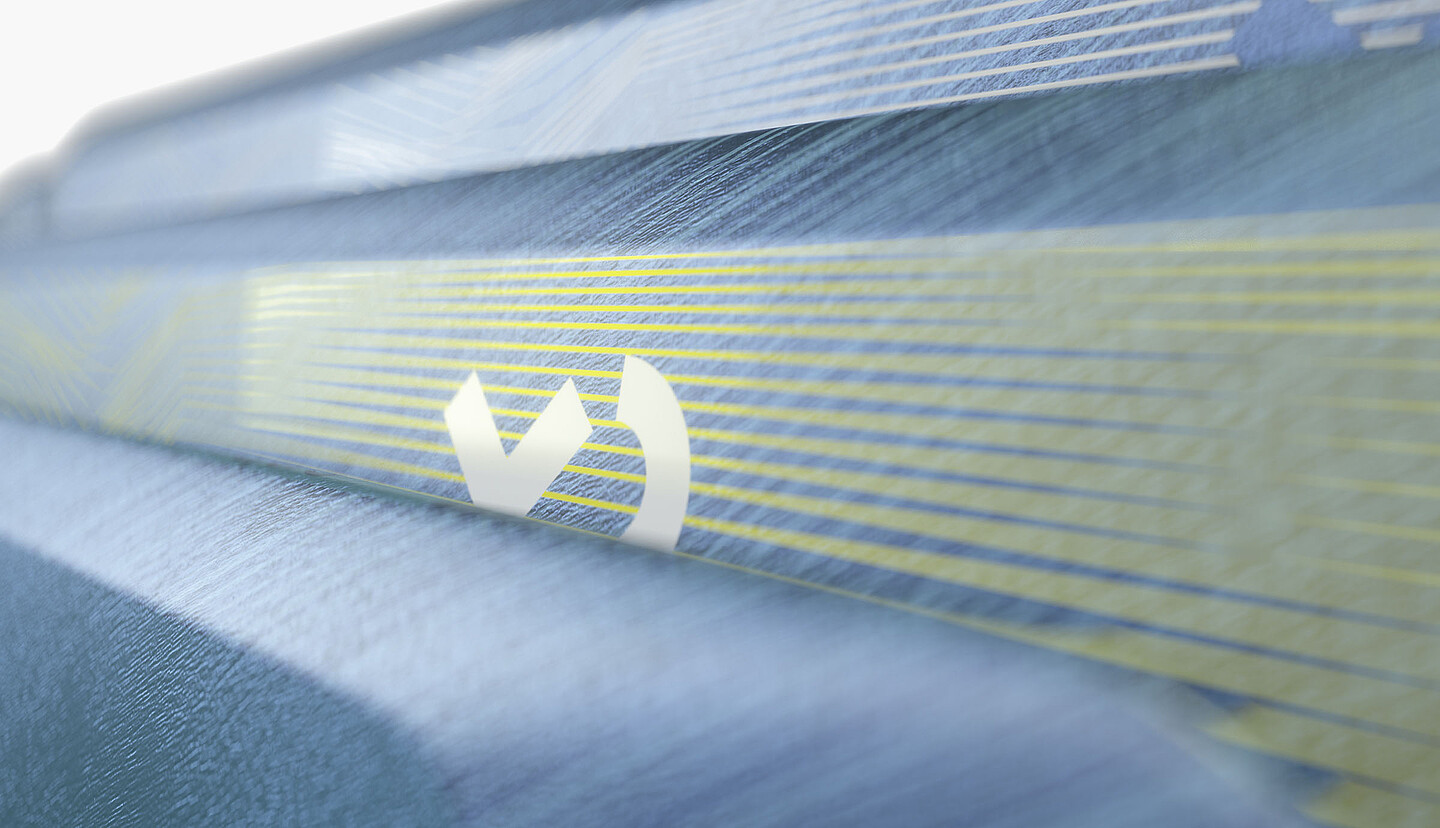
Decoration + Sensor Integration = IME
IME (In-Mold Electronics) combines decoration and touch functionality in a single highly efficient process. Transparent, conductive backing material for touch sensors is applied to the back of the component, while decorative designs are applied to the front side during injection molding. In this way, we translate your visions into surprising surface designs including functional touch controls.