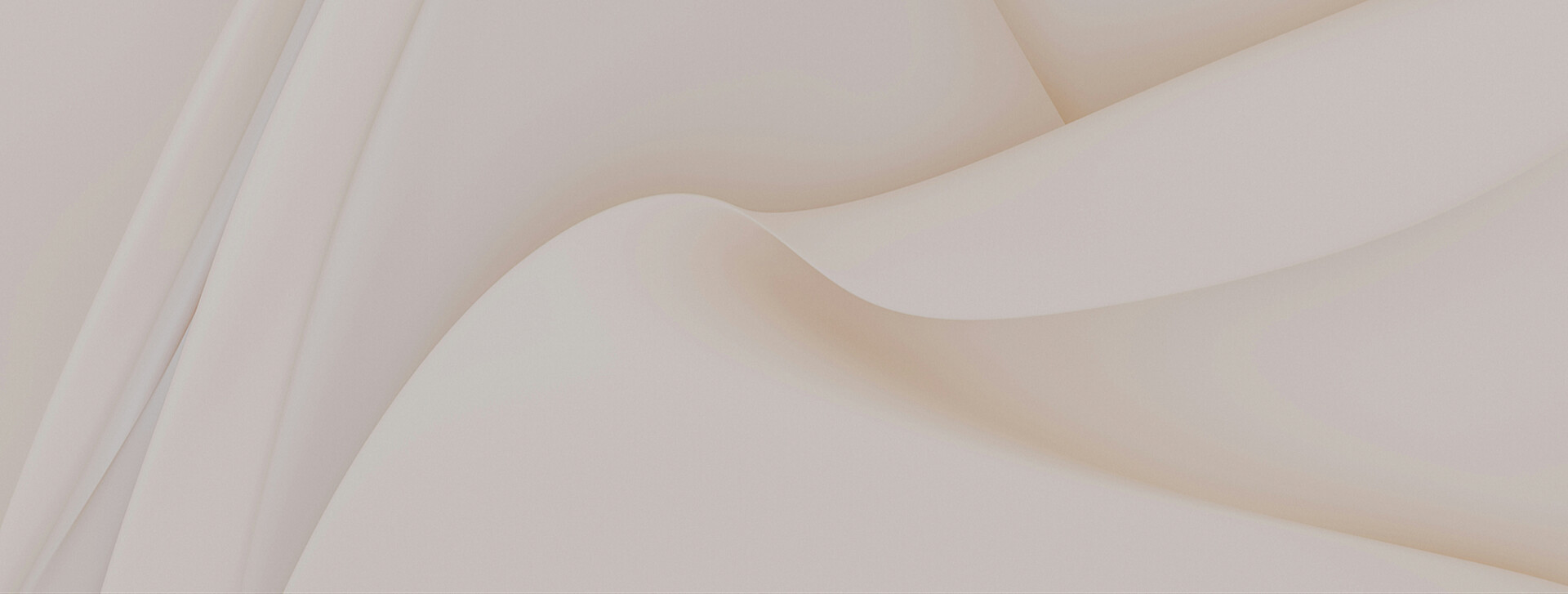
Press

Digital finishing of plastic tubes
Fürth/Germany, September 2nd, 2019: LEONHARD KURZ will be presenting individualized tube decoration in its most attractive form for the cosmetics and packaging industry at the K 2019 trade fair, from October 16 - 23 in Düsseldorf. KURZ, together with its subsidiary ISIMAT, have developed a process combining Indirect Digital Decoration (IDD) and digital metallization. This process enables variable data in luminous metallic colors to be applied simply and efficiently to plastic tubes.

Automated sensor integration live at K 2019
Fürth/Germany, August 19, 2019: At K 2019, LEONHARD KURZ will be demonstrating the automated integration of touchscreen sensors into plastic parts. The sensors will be applied to a white goods control panel using KURZ’s patent pending FFB (Functional Foil Bonding) process. The process was presented for the first time at Fakuma 2018 and is now being adopted in series production applications. A semi-rotary variant of FFB will be displayed at the KURZ booth for the first time.

LEONHARD KURZ produces study on the recycling of decorated plastics
Fürth/Germany, August 5, 2019: LEONHARD KURZ is presenting the results of a comprehensive study on recycling at K 2019, in the VDMA Circular Economy Forum. The in-house produced study examined the mechanical recyclability of plastic parts that have been decorated with surface coatings from KURZ. KURZ commissioned its development team to effectively support its customers in setting up a return and recycling system and in reducing their CO2 footprint. “Our customers need clear evidence that our surface decoration products do not affect the recyclability of their plastics. The scientifically sound study and our more than 120 years of experience in surface decoration enable us to effectively advise them in the development of their recycling concept,” explains Astrid Rauh, who works as a recycling engineer in the Environmental and Safety Management department at KURZ.

LEONHARD KURZ at K 2019
Fürth/Germany, July 18, 2019: LEONHARD KURZ is presenting at K 2019 from October 16-23 in Düsseldorf with a focus on new design and functional solutions for the automotive, consumer electronics, household appliances, and cosmetics industries.
Using a new process called IMD PUR, KURZ will demonstrate the combined use of IMD (in-mold decoration) and PUR (polyurethane) technology for automotive applications. A front panel will be decorated and overflooded with PUR in the same clamping unit on an Engel duo 2460/900 injection molding machine. The novel design effects that can be achieved with this process will be demonstrated at the trade fair booth by means of a radiator grill concept. Aside from having an avant-garde design, this concept also illustrates the technical feasibility of using the process for exterior applications. The cutting edge surface design of the demonstrator is equipped with functions for autonomous driving that were jointly developed with the LiDAR (light detection and ranging) sensor manufacturer Velodyne.
KURZ will also be demonstrating future-oriented concepts for automotive interior controls by means of a touch-control steering wheel – developed in a technological partnership with GE-T – with haptic feedback and freely programmable operating functions.

New IMD PUR dual-technology process for plastics decoration
Fürth/Germany, June 24, 2019: The coating manufacturer LEONHARD KURZ has developed a process for combining IMD (In-Mold Decoration) with PUR technology. In this process called IMD PUR, plastic parts are decorated during injection molding by means of in-mold decorating and then overflooded with PUR (polyurethane) within the same clamping unit. This produces sophisticated designs under a crystal clear, high-gloss surface. PUR layer thicknesses of between 0.3 and 15 millimeters can be created that exhibit a marked depth effect. Besides a glossy glass appearance, the PUR coating also provides a high level of surface protection. The decoration remains intact when subjected to scratches or stone impact, and the PUR topcoat is self-healing when scratched.

Concept door trim in speed racer design
Fürth/Germany, October 8, 2018: The coating manufacturer LEONHARD KURZ will be exhibiting an avant-garde design for automotive interiors in the form of a door trim concept at this year’s Fakuma. The plastic component will be produced at the trade fair booth B1-1105 of Sumitomo (SHI) Demag by means of an injection molding process with concurrent In-Mold Decoration (IMD).

Two designs plus functional integration in one shot
Fürth/Germany, October 1st, 2018: LEONHARD KURZ has developed a foil feeding unit for In-Mold Decoration (IMD) with two independently positionable foil webs. Using the patent pending IMD SI DUO feeding unit, it is possible to produce two plastic components with different single-image designs in one shot. At the KraussMaffei booth at Fakuma, two components will be manufactured on a PX 320 fully electric injection molding machine and individually decorated with the help of the IMD SI DUO. A touch sensor from the KURZ subsidiary PolyIC will simultaneously be integrated into one of the components by means of In-Mold Labelling (IML). KraussMaffei and KURZ will demonstrate an unprecedented level of IMD process rationalization with this live application.

LEONHARD KURZ wins Automotive Brand Contest
Fürth/Germany, September 24, 2018: LEONHARD KURZ was selected as a winner at the Automotive Brand Contest 2018. KURZ won in the Future, Mobility and Parts category. The jury of this international design competition for automobile brands was delighted by a door trim with interactive backlighting effects. The prize was awarded for the overall concept of the door trim including surface design, light effects, and touch functions.

Protecting originals made easy
Fürth/Germany, September 13, 2018: They look totally inconspicuous: barcodes printed by TTR (thermal transfer printing) in the usual black, on machine, automotive and replacement parts, on chemicals and building materials, on printed circuit boards and pharmaceutical packaging. But these barcodes might have secret inner workings. Because now they can be equipped with hidden, machine-readable authenticity features. By scanning these codes with a special reader, the authenticity of the labeled product can be verified unequivocally.
TTR Unique Verospec is the name of these thermal transfer ribbons with integrated, invisible counterfeit protection, developed by the coatings manufacturer LEONHARD KURZ. “We searched for an uncomplicated solution that can be integrated at little cost into existing manufacturing and labeling processes and is suitable for a wide variety of industries,” explains Bernhard Schmitt, product manager for thermal transfer solutions. “TTR Unique Verospec provides not only a secure, but also an easy means of revealing counterfeit products. That nobody other than our client can know about the labeling is an additional protection for the originals”.

World premier at Fakuma
Fürth/Germany, September 10, 2018: LEONHARD KURZ will be presenting for the first time ever at this year's Fakuma its patent pending FFB (Functional Foil Bonding) sensor integration process. This new process from KURZ provides a fully mechanical method of integrating touch sensors into plastic components. The integration of touch sensors into door trims will be demonstrated live on a newly developed machine from the KURZ subsidiary BAIER.

All four in one go: decorating, forming, backinjecting, punching
Fürth/Germany, August 24, 2018: LEONHARD KURZ hat das Verfahren IMD Varioform entwickelt, mit dem Bauteile in einem Schritt gefertigt und dekoriert werden können, für die aufgrund ihrer besonderen 3D-Geometrie bisher keine effiziente Dekorationslösung verfügbar war. Per IMD Varioform lässt sich für diese Bauteile jetzt die schnelle und flexible IMD-Rolle-zu-Rolle-Technik einsetzen. Bei dem einstufigen IMD-Varioform-Prozess wird direkt im Spritzwerkzeug dekoriert, umgeformt, hinterspritzt und ausgestanzt. Das Verfahren vereint IMD-, Umformund Stanztechnik. „Wir haben einen Weg gesucht, um etwas stärkere 3D-Formen wirtschaftlich zu dekorieren. Mit IMD Varioform schließen wir die Lücke und komplettieren unser breites Spektrum an Dekorationstechnologien“, erläutert Martin Hahn, verantwortlich im Bereich Application für Technology and Innovation bei KURZ. „Der Prozess ist hocheffizient und bietet ungeahnte Flexibilität in der Wahl von Oberflächendesign, Formgebung und Spritzgussmaterial. IMD Varioform ist die perfekte Antwort auf die steigenden Anforderungen der Produktentwickler und Designer.“

Soft touch meets visual design
Fürth/Germany, August 16, 2018: LEONHARD KURZ has developed a new product line for in-mold decoration (IMD) with a tangibly and visibly soft surface. These IMD coatings exhibit novel haptic properties while offering the same design and functional scope as KURZ’s general products for the IMD process. The haptic and visual designs are transferred in a single process step during the injection molding process. Whereas a velvety haptic effect has previously been reserved for single-color designs only, the new coatings can lend a soft finish to leather designs, or a robust grip to bold color gradients.

HMI solutions for the future
Fürth/Germany, August 2nd, 2018: Seamless automotive cockpits controllable by touch or gestures, household appliances with a stylish dead front look and hidden control panel, plain surface finishes that reveal mood-setting backlit designs when approached – LEONHARD KURZ will be presenting latest generation HMI applications at Fakuma. Visitors to the KURZ booth A4-4122 will be able to see a comprehensive range of surface decoration solutions, sensor technologies, and industrial sensor integration applications that offer scope for innovative HMI design and functionality.

HMI concepts seamlessly combined
Fürth/Germany, May 24, 2018: Automotive cockpits with seamless, continuous instrument panels, homogeneous surfaces with a dead-front effect that reveal backlit designs or controls in response to a hand gesture – the coating specialist LEONHARD KURZ will be showing what the car interiors of the future will look like at this year’s Automotive Interiors Expo from the fifth to the seventh of June in Stuttgart. Visitors to the KURZ booth will be able to see innovative HMI (Human Machine Interface) applications, for example a multifunction steering wheel with optional selectable functions, which can be controlled by means of a multi-touch sensor with haptic feedback. A further highlight is a decorative trim with a day/night design: During daylight the viewer sees an elaborate surface design with various matte finish structures. A touch button activates partial backlighting, a touch slider changes the light color and intensity. Also on display will be a seamless dual touchscreen, a multi-touch pad with a wide variety of IMD (In-Mold Decoration) designs to choose from, and a touch-controlled air conditioning system.