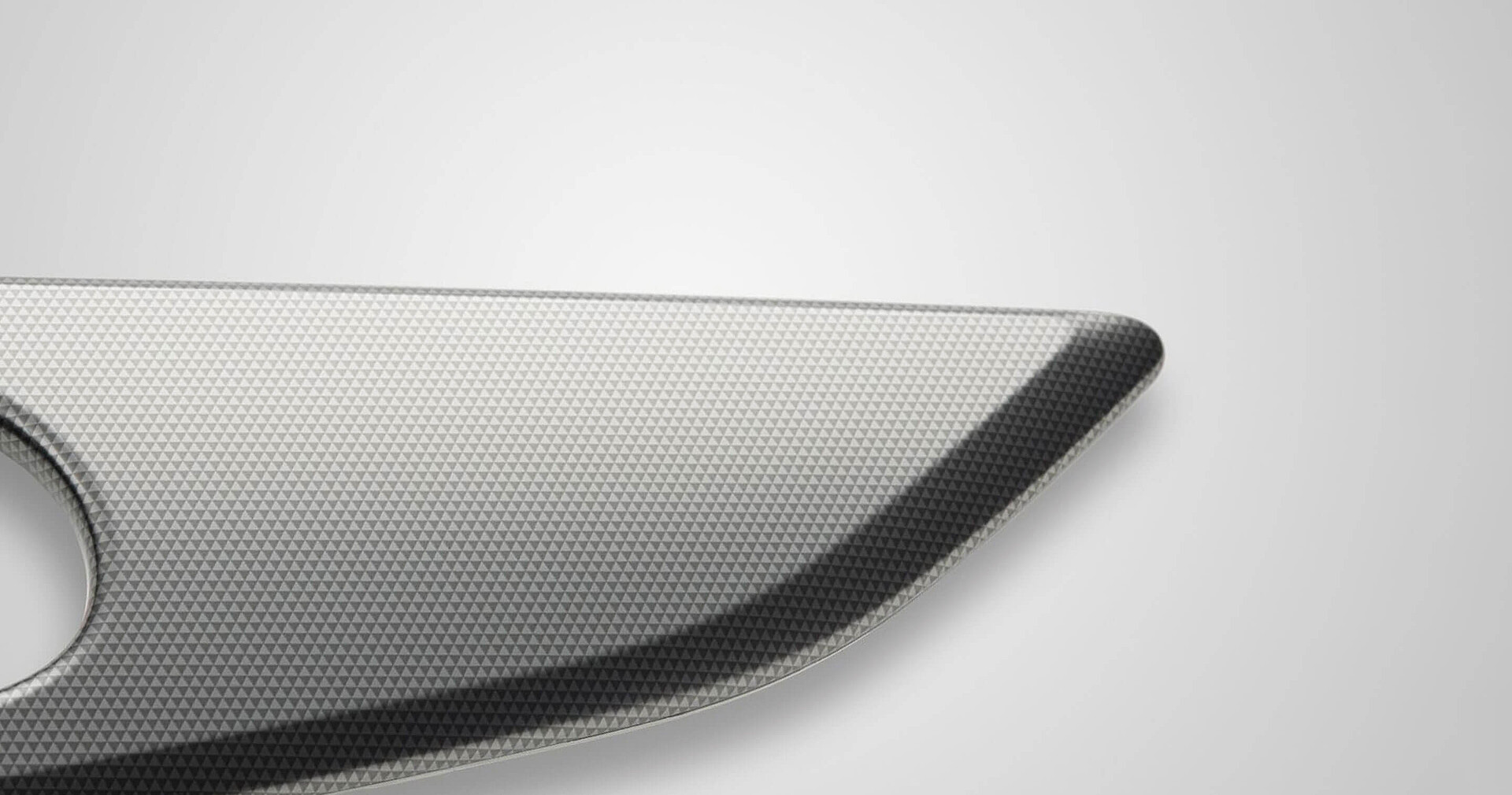
Insert Molding Decoration
Insert Molding is perfect for the economical finishing of curved and multidimensional parts such as sound boxes or household robots. This process allows several production steps to be completed in one pass: Hot Stamping, vacuum or compressed air molding, plastic injection molding, and precision cutting.
Process
- In the production cell, the already decorated component sheets are deep drawn by vacuum or compressed air
- They are then cut out to make room for control panels or designs, for example
- The inserts then reach their final station, where they are back-injected
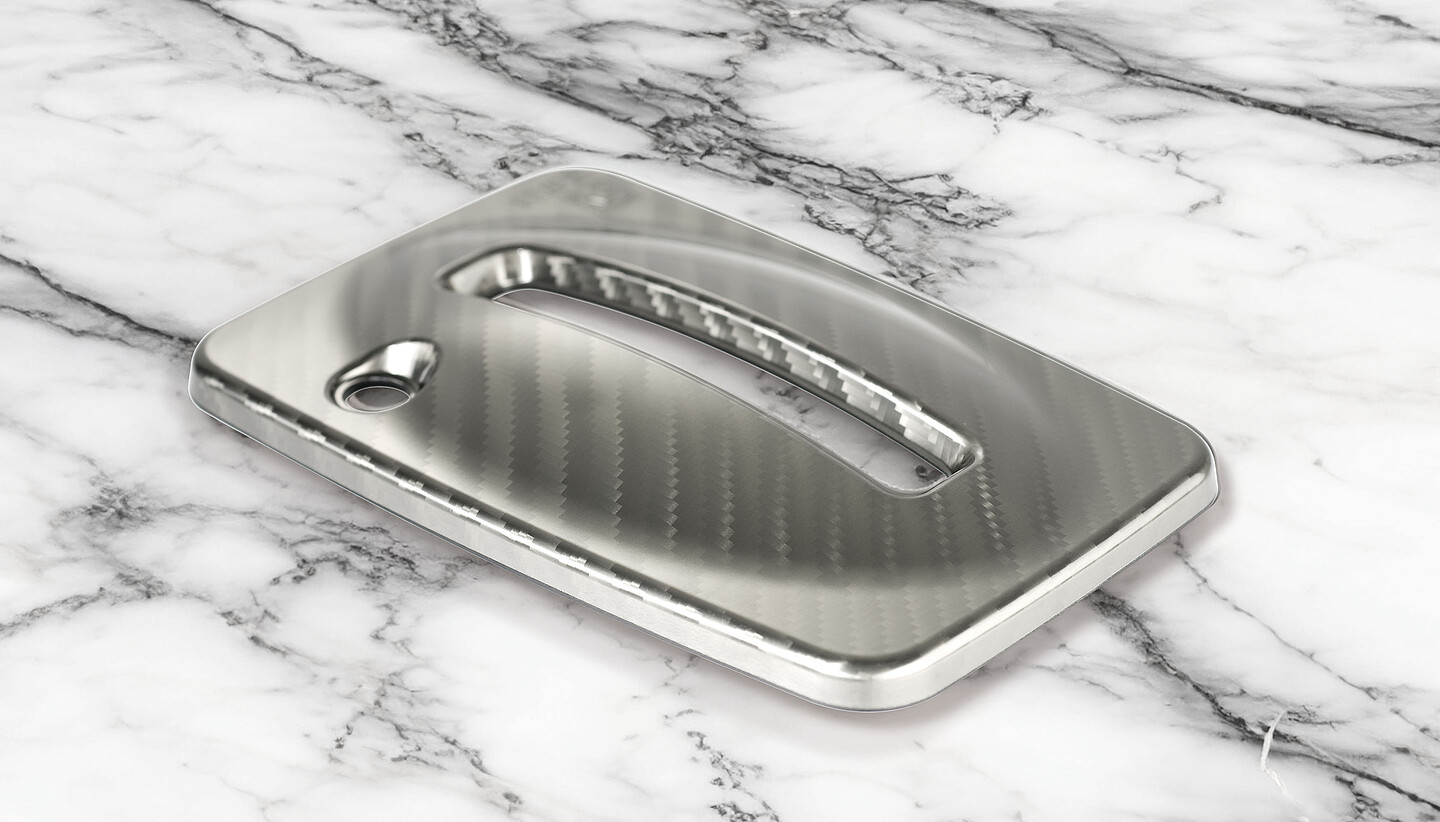
Significant advantages of KURZ Insert Molding:
- Economic process, suitable for your specifications
- CO2 reduction by combining several production steps in one process
- Suitable when using recyclables
- Diverse design options, because a wide variety of endless designs or single images can be produced
- Sensual effects can be realized, with tactile designs, day-night design and backlighting
- Combinable with PolyTC® sensors, which are ultra-thin, easy to shape, and highly transparent due to their silver-based metal mesh structure
- Maximum freedom of design, as keys and switches can be eliminated and deep drawing allows a wide variety of organic shapes